We understand just how daunting it can be knowing that you may need to implement a barcode system in your warehouse, but you can rest assured it’s actually much simpler than you may have feared! Here, we discuss how to decide if your business does need a barcoding system, and how you can implement one.
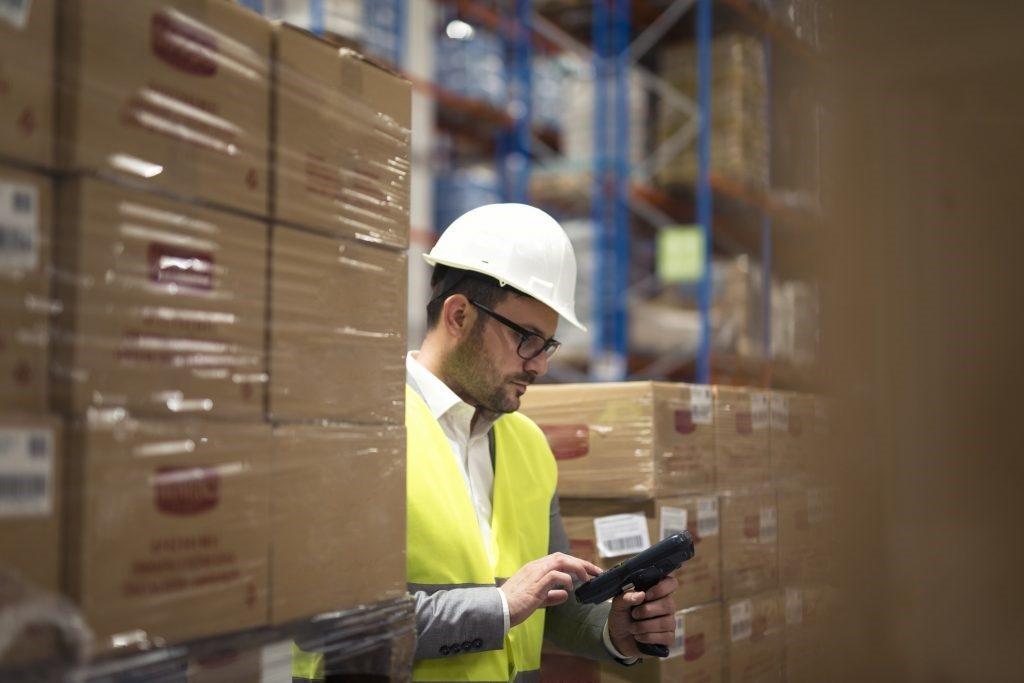
Do I Need A Barcode System?
Before diving straight in and beginning to look for a supplier to implement a barcode system within your warehouse, it’s worth considering if your business will definitely benefit from installing one. Whilst the answer to this question is usually ‘yes’, it’s always worth pausing for a moment and considering all of your options, as installing a barcode system in your warehouse takes time and takes considerable investment.
Here are just a few of the main reasons that you may need a barcode system in your warehouse:
- You’re maintaining MRO inventory
- Your vendors and retailers require barcodes to purchase from you
- You warehouse your inventory and therefore need to keep a close eye on stock counts
- You’re struggling to keep accurate records of stock levels, or they are taking far too long to complete
If you have fully considered if you need a barcode system in your warehouse, you can now move onto the next step and begin laying the foundations for installing one within your premises.
How To Set Up A Barcode System In Your Warehouse
Now that you’re completely confident that your business definitely requires a barcoding and stock management system, you will probably have a million questions on how to set up a barcode system within your warehouse. Whilst it can be quite daunting at first, we have put together a few simple steps that you’ll need to take in order to minimise the stress when it comes to setting up a barcode system within your place of work.
List All Items Within Your Inventory
Your first port of call should be making a list of all of the items in your inventory, this will help to make an itemised list of all of your products and best prepare you for your newly installed barcoding system.
If you stock a large range of items that are similar, then this is a fantastic way to ensure you are able to differentiate between them properly when it comes to barcoding. To guarantee you are doing everything you can to minimise errors when your system does come in, we would recommend including the following information in to your database spreadsheet:
- Item dimensions
- A short physical description of the item
- Total cost of purchase
- The minimum amount of said item that you require in your inventory
- Any vendor information
Choose Your Preferred Barcoding Software System
There are a number of barcoding software systems on the market currently, and as with everything, some are better suited to certain businesses and industries than others. Variables such as the size of your business, how much you sell on a daily basis and the type of stock you carry, will all come into play when you’re considering what barcoding system is right for your requirements.
We would recommend using G-Smart Stock for warehouse solutions as this system enables your business to have a fully functioning warehouse management system which you can manage online. This software allows you to marry up your warehouse barcodes with your mobile scanner and database system, essentially making your operations a fully web-based inventory management system.
If you don’t have the technology, it’s not a problem as GSM Barcoding have a stock management solution for any business, no matter what set up you have internally.
Depending on your company’s requirements, you’ll find that some barcoding systems are capable of actually creating barcodes for your items too. So, if you’re starting completely afresh and need a full barcoding and stock management solution, this may be your best bet.
Choose Your Barcode and Create Them
Depending on the type of industry you work in, you will require a specific type of barcode. Now that you have you barcode system installed, you will want to choose from one of the following types of barcodes, depending on your requirements:
- Two-Dimensional – The most common type of this barcode is QR codes, which are powerful barcodes capable of containing around 7,000 characters in one code. These are best suited to very specific types of products that require a lengthier product description included within the barcode.
- One-Dimensional – Utilising variable width lines and spaces to encode data, this type of barcode is limited in data storage to only a few dozen characters. This is best suited to products that are more general and easier to categorise.
- Numeric – This particular barcode is usually used in retail, warehousing and industrial settings. It is the most common type of barcode and is used in the vast majority of industries.
- Alpha-Numeric – These codes are somewhat similar to numeric barcodes, and are commonly used in military, automotive factories and on grocery shelves.
Once you’re confident that you have chosen the perfect barcode for your needs, you can begin creating and printing them.
Update Inventory Management and Add Your New Barcodes To Products
All that is left to do now is to ensure that your inventory management system is updated with your new barcodes and then to begin adding them to the products in your warehouse. You can now enjoy your brand-new barcoding system and begin reaping all of the benefits that come along with having one!
If you are looking for any assistance to help install your barcoding systems, then please don’t hesitate to get in touch with the team at GSM Barcoding. We have over 40 years’ experience in the industry, so you can rest assured that our experts can advise you on every aspect of installing a barcode solution in your warehouse.
If you would like further information about how we can help you, then please don’t hesitate to contact us today. We look forward to hearing from you soon!