It is a fundamental truth of business that productivity in operations management can significantly impact an organisation’s efficiency, profitability and success. But what is productivity? It’s a term we often use but don’t always fully understand. In this blog, we will explore the concept of productivity and how organisations can improve it.
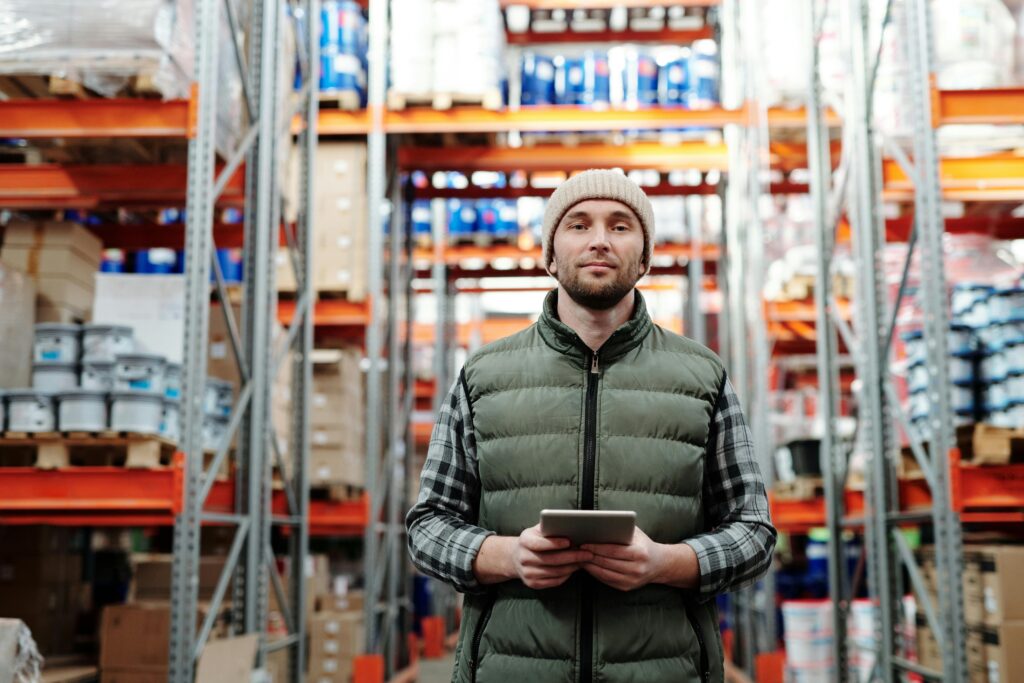
Understanding your productivity requirements
Productivity is the key measure of efficiency. It involves optimising resources within a business, transforming them efficiently, and maximising output. The greater the efficiency, the more competitive a business can be in delivering higher profits or enabling lower prices.
“Productivity is how much output for a given input”
For organisations, there may be many aspects of productivity that they can optimise, including employee time management, customer service productivity and of course operations productivity. In this blog we shall focus on this last one: how do organisations optimise their operational productivity?
Getting to grips with productivity
By measuring and comprehending efficiency KPIs organisations can identify efficiencies within their operations, develop strategies to deal with deviations and improve overall productivity. Key productivity measures include labour hours, capital employed, and goods or services produced. Efficient use of resources such as labour, capital invested, and stock ensures that organisations achieve maximum output while minimising costs, creating sustainable growth and performance.
How to measure productivity
Organisations can deliver improved productivity through operations measurements that identify bottlenecks and optimise resources for effective output. There are various tasks and processes within operations management where measurement of labour, technology investments and material usage can be applied.
- Goods in– KPI Measurements can include, the percentage received on time and in full, and the speed and accuracy of inbound stock checked and cleared.
- Put away – Once received, stock is allocated to storage areas. Speed and accuracy are key with the replenishment rate KPI used to measure performance.
- Processing – Overall throughput including units’ production per hour and error rate are all important KPI metrics for manufacturing, kitting and assembly.
- Picking – Inventory accuracy, pick per hour and the right-first time (RFT) measurement for accuracy are key to ensuring efficient operations.
- Dispatch – KPI includes order fill rate, how quickly goods can be sent out and the cost of dispatch per unit.
Many metrics can be used, and they can vary depending on the industry sector and the strategic priority of the organisation. KPIs should cover the full range of inputs and outputs measured over time to get a fair and true view of productivity within the organisation and compare it to the industry average. By measuring productivity operations managers can quantify their productivity levels accurately and invest in technology such as barcoding, and workforce training that can boost productivity.
Drivers of productivity in operations management
There are several key drivers of productivity in business, which can be broadly categorised into people, technology, and planning. It is recommended to focus resources on these areas and develop strategies to achieve more efficient operations, ensuring that the resources invested produce a return on investment (ROI).
People
An efficient team comprises motivated staff that feel empowered to do their job and supported by management. It may not immediately seem like an operation manager’s top priority, but unmotivated teams lead to higher staff turnover, increased mistakes and slow processing of operational tasks.
The warehouse and manufacturing sectors have one of the highest staff turnovers in industry, this fact, results in resources being dedicated to recruitment and onboarding, slowing productivity and costing the business money. Some steps can be taken to improve employee efficiency in operations including having an effective training programme to empower and release capabilities and maximise worker productivity.
Technology can play a role in effective staff training and retention, such as with Android handheld devices that enable staff to onboard quickly with familiar tech while accessing apps and documents and communicating with colleagues, improving communication, processing, and safety on site.
Technology
Technology drives step changes in productivity that can disrupt entire industries, leading to new workflows and practices, cost structure changes and impacts on profitability. Historically technological changes such as the steam engine in manufacturing, electricity and the Internet have transformed productivity so much that they have altered entire societies and how we live and consume products.
For businesses to achieve productive competitiveness they must adopt those technologies that improve key areas of operations, including accuracy, traceability and speed that lead to efficiency. The technology drivers with the greatest impact on operations management include:
- Wireless Networking
- Data Capture (Auto-ID)
- Mobile devices (mobile computers, tablets, printers)
- Computer Software
- Robotics
- AI & ML
Many emerging technologies are set to create vast changes in operations productivity, including AI and Machine Learning, Robotics and Augmented reality (AR). Organisations that can adopt and implement these technologies effectively will reap productivity benefits that can produce a sustainable competitive advantage over their competitors and lead to transformational shifts in their industry.
Planning – Workflow Design
Intelligently designing and applying the best work methods can greatly boost operations efficiency. Operations management principles such as Kaizen, JIT and six sigma can create a productive environment in which resources are utilised efficiently and productive capacity optimised, so inputs are received at the right time and production is completed with zero defects.
“Workflow planning coupled with technology delivers maximum efficiency”
The design of the workflow in business operations has a direct impact on efficiency through resource allocation and waste reduction. Simple yet effective strategies can include:
- Allocating promotional and fast-moving items closer to the picking station
- Optimising seasonal put-away locations.
- Scheduling deliveries better for speedy processing and put-away.
More technically complex strategies may involve a warehouse management system (WMS) or a Material resource planning (MRP) system in combination with automated conveyor systems, pick-to-light systems, and the latest technology in warehouse robotics, such as fetch and retrieval robots, aiding the most labour-intensive human activity of walking around the warehouse and moving items to picking stations.
Implementing advanced workflow in operations requires the right technology partners and experienced consultants. At GSM Barcoding we work with leading technology providers such as Zebra and Honeywell, plus software developers to create the latest leading productivity-enhancing solutions for operational challenges. For more information or a free consultation speak to one of our advisors, and we will be happy to help.